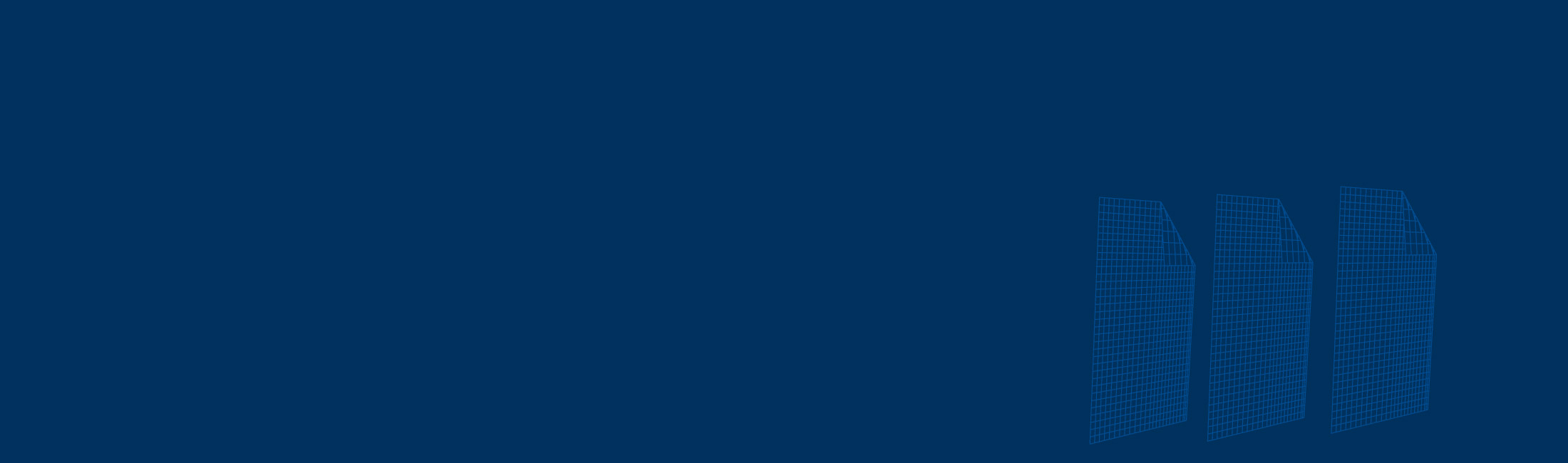
Q&A
AGC材料を使用した受託製造に携わる方へのQ&A
-
積層板は何度も高温にさらされると、変色や着色の問題が起こりますか?
- どの積層板も、高温サイクルを何度も繰り返すと黒ずんできます。その程度は、サイクルの温度と時間に依存します。分解温度に近い温度にさらされた積層板は、低温にさらされた積層板よりも黒ずんでいきます。ソルダーマスクの変色効果により、下にある基板の変化が見えにくくなる場合があることに注意が必要です。
- 積層板は、化学物質で汚染されていない限り、通常、高温に何度もさらされた後でも変色することはありません。水溶性フラックスの中にはシミの原因となるものがあり、またソルダーマスクも特定のフラックスで処理した後は、高いイオン汚染レベルを維持してしまうことがあります。
- ソルダーマスクの表面に円形の斑点や渦巻き状の白濁した汚れが発生した場合、通常、220 ºF / 104 ºC で約 2 時間のポストベーキング処理により取り除くことができます。
- 積層板を積層する際にAOI装置の検出におけるコントラストが問題になる事はありますか?
- 通常、ほとんどのAOIによる検査はソルダーマスクのコントラストに依存するため、積層する際に積層体が黒ずんでも、検査工程に悪影響を及ぼすことはありません。
- AOIの検出原理として反射率や蛍光発色を利用している場合も、その検出効率は色の変化にはほとんど影響を受けません。
-
積層板は、パネルや完成基板の反り量に寄与しますか? 積層板は、様々な方法でPCBの反りに寄与することがあります。
- まず、基板がアンバランスな構造で構成されている可能性があります。これは一般に、基板を構成する層の数が奇数であったり、基板の中心面のどちらか片側に誘電体層が偏っていたりする場合に起こります。
- 次に、ボードはバランスよく作られていても、コア自体が非対称で、異種のプリプレグが使用されていることがあります。例えば、0.005インチのコアは、2116のガラスクロス単層、1080のガラスクロス2層、または2113と1080のガラスクロス層で作ることができます。後者の場合、2枚の異種プリプレグの配置が基板の中心面の両面に適切に分布していないと、反りが発生する可能性があります。
- 基板やパネルにおける銅配線の分布も反りの原因になります。設計者は、反りを最小にするために、ボードの中央に対して銅配線のバランスをとるようにすべきです。また、製造者は基板を作るときに湿気や空気を排出する能力を犠牲にしない様に、積層板における銅配線をバランスさせる通気パターンを採用する必要があります。
-
基板を高温にさらすと、PCB 製造時や組み立て時に反りが発生することがあります(特に表裏で厚みに勾配がある場合)。反りは、多層板の積層サイクル中にも発生することがあります。また、基板工場での HASL工程時や組立時のリフロー時にも発生することがあります。リフローでは、プロセスパネルの厚み、パネルサイズ、基板重量が反りに影響を与えることがあります。
-
積層板の熱膨張係数はどのようなもので、積層工程にどのような影響がありますか? 熱膨張係数は、温度変化による寸法変化です。
- 各積層板は、X、Y、Z軸の熱膨張係数(CTE)が異なる場合があります。特にX軸およびY軸のCTEは、使用する補強材の影響を最も強く受けます。Eガラスで製造された積層板の場合、CTEは通常12 ~ 16 ppm/°Cです。
- Z軸のCTEも重要です。補強材によって積層板がX軸とY軸に拘束されている場合、熱にさらされるとZ軸に沿って積層板が膨張します。当社は一般的に、基板の温度を50°Cから288°Cに上げたときの膨張率の変化としてこれらの差を報告します。膨張量は、基板設計、樹脂の種類、および補強材によって異なります。その量は1.5%と低い値から7%近くの高い値まで様々です。当然のことながら、層数の多い基板や厚い基板では、Z軸の膨張が大きくならないようにする必要があります。さもないと、熱サイクル試験の際に信頼性の問題が発生する可能性があります。典型的な欠陥は、バレルクラック、層間剥離などです
-
ウェーブはんだ付け工程は何か積層板に影響を与えますか?
- ウェーブはんだ付けは、その工程が適切に制御されていれば、積層板にほとんど影響を与えません。
- 層間剥離を避けるためには水分の取り込みを考慮する必要があるため、ウェーブはんだ付けの前にプリベークすることをお勧めします。
-
インライン/オフライン洗浄プロセスは何か積層板に影響を与えますか?
- 無加工の積層板は、加工した基板(ソルダーマスクで覆われたもの)よりも一定時間内に多くの水分を吸収してしまいます。さらに、基板やパネルの洗浄頻度および洗浄時間も各積層板の吸湿に影響を及ぼします。
- 適切に保管されていた積層板で洗浄サイクルが短く、直ちに次の工程に進むのであれば通常は問題ありません。
- 耐薬品性の確認をしてください。(けん化剤、アセトンなど)
-
積層板はどのくらい湿気に敏感ですか?
- 積層板の吸湿量は、温度、湿度、工程の継続時間によって異なります。当社では通常、IPC標準規格を使用して積層板をテストしています。
- 各積層板製品によってそれぞれの吸収率が異なることにも注意が必要です。これは、リフロー工程やウェーブはんだ付け工程のような高温になる作業において、剥離の原因となる水分を取り除くために、ある積層板は他の積層板より長くベークする必要があるため、重要なポイントです。
-
基板(積層板)は何回程度リワークできますか?
- 回路基板が許容できるリワークの回数は、いくつかの要因によって異なります。使用されている材料の種類はひとつの明白なポイントですが、銅箔の剥離強度、加えられた熱、与えられた機械的な力、パッドサイズ、基板サイズ、基板重量、銅配線の分布、層構成、厚さなども重要なポイントになりえます。
- リワークに起因する問題を低減するために、積層板は製品パンフレットで指定されている特性、特に最高暴露温度(リフロー・ウェーブはんだ付け、手作業でのリワーク)に基づいて処理される必要があります。
- 低いCTEを持つものや、Tg、T260、T288、T300で示される高温下の剥離時間等で高い熱安定性を示す積層板ほど、複数回のリワークサイクルでより良い性能を発揮します。
-
積層板をさらすことができる最高温度と持続時間は?
- 積層板は製品パンフレットで指定されている特性、特に最高大熱暴露温度(リフロー・ウェーブはんだ付け、手作業でのリワーク)に基づいて処理される必要があります。
- しかし,暴露時間や回路の構造など,いくつかの要因が最高使用温度に影響を与える場合があります。これらの要因がある場合、RTI(相対温度指数)とMOT(最高使用温度)を考慮することが、最良の結果を得るために重要です。
-
積層板は何回の温度サイクル試験に耐えられますか?
- 積層板は、熱サイクルが適用されるたびに劣化します。温度が熱分解温度に近づくほど、劣化プロセスは速くなります。低温でも劣化は進行しますが、その速度は遅くなります。
-
銅箔の剥離強度がリワークに影響するのはどのような場合ですか? パッドは何回くらい、またどのくらいの温度でリワークできますか?
- リワークの必要条件は、銅箔の剥離強度、加えられた熱、機械的な力、パッドのサイズ、リワーク方法などのいくつかの要因によって異なります。
-
積層板の耐薬品性の重要性とは?
- 基板の洗浄(クリーン、ノークリーンフラックス)には、耐薬品性が重要になる場合があります。洗浄工程で特定の化学物質が混入すると、性能低下の原因となることがあります。しばしば基板が汚染され、それは人間の目では検出不可能です。このような汚染は、実使用下での障害の原因となるため、避ける必要があります。インライン/オフライン洗浄を行う場合、使用する洗浄剤を慎重に検討することが非常に重要になります。一般的には、純水とアルコールが適しています。
-
積層板の特性は、組み立て工程におけるスコアリング(切り線形性)やブレイクオフ(個片化)にどのように影響しますか?
- 一部のパネルは、ある時点で個片に分割する必要があります。その際パネルのサイズ、厚み、重量、積層されたパネルの総重量、またはスコアリングの深さによっては、個片化が組み立て工程をより困難なものにする可能性があります。
- 積層板の中には、熱を加えると柔らかくなるものがあり、それがパネルの安定性に影響を与えることがあります。あるパネルのサイズや厚みに対して、特定の取り扱い方法(例えば、設置のための中間サポート、リフロープロセスなど)を決定する必要がある場合があります。一般的には、機械的特性を確認し、追加の取り扱い手順が必要かどうかを判断することをお勧めします。
-
積層時の層間剥離の根本的な原因は何ですか?
- 層間剥離の根本的な原因は、プレス時の圧力不足、積層板の吸湿、プリプレグやコア表面の汚染(オイル、グリースなど)、ビアへの水分の巻き込み、積層板の硬化不足、酸化処理やデスミア処理等の化学反応工程の最適化不足である場合がほとんどです。
- 最も接着力の弱い界面は、銅の酸化表面とプリプレグの間の界面です。ほとんどの剥離はこの界面で発生します。Rev. 02-21
- 通常、積層環境では、吸湿と高温サイクルが組み合わさると、層間剥離が発生する可能性があります。
- 一般的に、高い Tg、高い分解温度、低い Z 軸-CTE、優れた T260、T288、または T300 特性を持つ積層板は、複数回の高温サイクルに対して優れた特性を示します。
-
鉛フリーはんだを使用できる積層板はどれですか?
- 特定の材料が鉛フリーはんだに対応しているかどうかは、基板製造プロセスの詳細が非常に重要な役割を果たします。銅メッキの厚みとPCBの吸着水分量は、考慮しなければならない多くの事柄のうちの2つです。
- 高温を必要とする鉛フリーはんだ付け工程では、HDI設計の属性を認識することが重要です。例えば、PTHのサイズ、ホールとホールの距離、層数などは、製品の性能に影響を与える可能性があります。
- 一部の非常に古い材料グレードを除き、すべてのAGCマルチマテリアルの積層板とプリプレグは、設計とリフロー条件によっては、鉛フリーはんだに対応しています。
-
プリント回路の製造および組立
- 完成したプリント基板(PCB)の保管方法は、後の工程で問題なく使用できるようにするために重要であり、決して軽視できません。今日、市場にはさまざまな樹脂システムがあり、それぞれが異なる速度で水分を吸収します。
RoHS指令の施行や鉛フリーはんだ(SnPbからSAC305)の増加により、リフロー温度が220℃から260℃へと上昇し、回路基板が高温にさらされると、吸収した水分の蒸気圧が大幅に増加します。この高い蒸気圧は、SMTやウェーブはんだ付けの前に除去しないと、PCBの層間剥離やクラックの原因となることがあります。水分の更なる吸収を制限するために、製造されたPCBは、帯電防止層を有する承認された防湿袋に入れて出荷することをお勧めします。
どのような包装が製造された基板に最も適しているかは、様々な要因によって決まります。これには、PCBの保管条件、積層板の材質、最終的なメッキ仕上げ、基板全体の厚さなどが挙げられますが、これらに限定されるものではありません。窒素ガスと一緒に乾燥剤パックを追加することで、吸湿を最小限に抑え、基板の表面仕上げを、はんだ付けしやすい状態に維持することができます。包装内に湿度インジケーターカードを同梱することで、包装を開封した際の視覚的な証拠とすることができます。
N2ガスを導入した直後に、適切なヒートシール装置を用いて防湿性の袋を密封する必要があります。袋を開けた後は、吸湿を制限するために、外気への暴露を制限する必要があります。乾燥包装は、袋がJEDEC-STD-033基準に従って400°Cおよび90% RHを超えない貯蔵室環境に保管されている場合には、1年間の使用寿命まで吸湿を制限できるものである必要があります。
有鉛と鉛フリーの両方のはんだ工程で使用されるプリント基板は、最適な性能と信頼性を得るためにプリベーキングを推奨します。ただし、このベーキングがはんだ付け性に悪影響を及ぼさないかどうかについては、薬品供給元にご相談ください。前述したように、樹脂の種類によって吸湿速度が異なります(特にポリイミド樹脂)。また、プリント基板の設計、レイアウト、金属仕上げの状態によって、必要なベーク時間を決定します。例えば、全面にメッキが施された基板は、閉じ込められた水分を除去するために非常に長いベークが必要な場合があります(可能であれば)。
積層の前に、適切な空気の流れを確保するために、コンベクションオーブンで基板を*ベーキングすることをお勧めします。PCBの水分を除去するための最小ベーク時間を決定するためのガイドラインを以下に示します。場合によってはより長いベーク時間が必要な場合もありますが、はんだ付け性に悪影響を及ぼす可能性があります。
OSP/無電解スズ: 110°C ~ 120°C(230°F ~ 250°F)で1 ~ 2時間
ENIG/無電解銀: 150°C(300°F)で4 ~ 6時間
* PCBはラック上に配置し、積み重ねないでください。スタックの中ほどにある基板が、適切な水分除去を可能にする最低温度に達しない場合があります。
適切にプロファイル設定され、較正されたリフローオーブンは、あらゆる手作業のはんだ付けと共に、高信頼性の完成されたPCBを達成するために欠かせません。後日、二次または後はんだ付け工程を行う基板は、適切な防湿袋または窒素キャビネットに保管し、再度密閉する必要があります。
本書に記載されている情報は、信頼性が高く正確であると思われます。しかし、最終的な結果に影響を与える多くの要因があり、信頼性の高いPCBを得るために、どのようなプロセスが製造オペレーションに最も適しているかは、個々のお客様によって判断される必要があります。
- 完成したプリント基板(PCB)の保管方法は、後の工程で問題なく使用できるようにするために重要であり、決して軽視できません。今日、市場にはさまざまな樹脂システムがあり、それぞれが異なる速度で水分を吸収します。